Local 1245 members keep PG&E’s largest gas storage facility safe and secure
As temperatures plummet and winter frost hits the air, millions of Californians are quick to turn on their gas-powered heaters – and few stop to think about the billions of cubic feet of gas needed to keep California’s homes, businesses and other buildings warm through the chilly season.
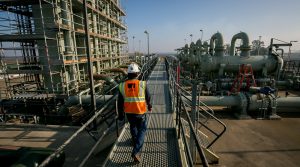
One of McDonald Island’s two processing stations
But the IBEW 1245 members who work at PG&E’s McDonald Island gas storage facility think about it every day, and the arrival of colder weather signals that it’s time for their facility to switch over from procurement mode to disbursement mode.
“During the summer, we’re mostly buying, storing and injecting gas into the [storage cavern]. And then in the winter, we’re usually pulling the gas out to meet the needs of the customers,” explained Gas Control Technician John Koga. “But sometimes we have to switch it up, for instance if we get a big order of gas in from Canada during the winter.”
Situated on a tiny, relatively remote island in the Sacramento-San Joaquin River Delta just west of Stockton, McDonald Island is PG&E’s largest gas storage facility, and the Local 1245 members employed there work day in and day out to ensure that millions of Californians have access to the gas they need when they need it, while also keeping the plant in tip-top shape.
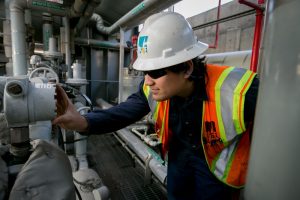
Gas Control Tech John Koga checks a gauge
“We do instrumentation, controls, and electrical work to maintain the gas storage facility and the natural gas compressor stations,” Koga said, explaining the roles and responsibilities of his department. “We deal with a lot of different systems, and new technology is always coming out, so we’re trying out new equipment, different types of programs and different control systems. We get to do a lot; I think it’s a really great job to have.”
Island Life
Hidden 5,000 feet below fields of growing potatoes and asparagus, the core component of the McDonald Island facility is the one few people ever see — the massive underground cavern where the gas is stored until it is needed. On the surface, two gas compressor stations (one of which is being rented by PG&E from another company) inject the gas into the cavern, and two gas withdrawal/processing stations pull the gas out, measure it, and feed it into cities and towns all across PG&E’s service area. With a maximum capacity of 82 billion cubic feet (BCF), McDonald Island is capable of providing 25 percent of Northern California’s winter peak-day gas demand.
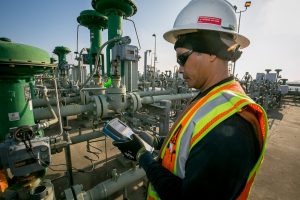
Gas Control Tech Quyen Ha troubleshoots an issue with a valve
The Utility Reporter caught up with Koga and his team as they worked through their yearly maintenance inspection on one of the processing stations. After donning the required personal protective equipment, including two sets of gloves and a specialized helmet with a face cover, Koga de-energized the main breaker on the variable frequency drive (VFD) unit, and then double-checked it to ensure that it would be safe to inspect that particular motor.
Down on the lower level of the same station, Gas Control Technician Quyen Ha used a digital valve controller to troubleshoot a minor issue with some of the valves that control the flow of the gas coming out of the natural gas wells. There are 87 such wells on McDonald Island, and the corresponding valves need to be checked and calibrated regularly to ensure that they continue to operate properly.
In The Office
Like most yards, the McDonald Island team has its own dedicated support staff working behind the scenes to manage the paperwork.
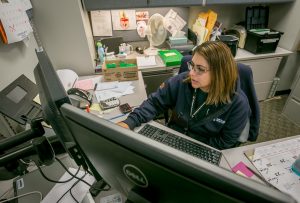
Senior Maintenance Assistant Linda Sendig
“I do payroll, order materials, keep track of valve cards and records on site, that type of thing,” explained Senior Maintenance Assistant Linda Sendig, noting that many of her responsibilities are similar to those of an Operating Clerk. “But with my classification, I’m on the physical side, and that means I can also operate the forklift. So if we get heavy duty deliveries, I can offload, unload, and deliver materials to other yards if needed.”
Sendig enjoys the fact that her job affords her the opportunity to expand her horizons and get a better understanding of the system that she helps to maintain.
“In the few years that I’ve been here, I’ve been learning more and more about gas pipeline and the materials that are used to keep that pipeline operating safely,” she said.
Under Control
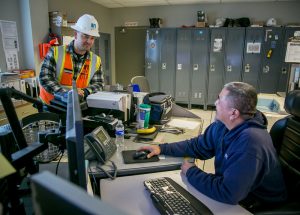
Gas Control Tech Hugo Gonzalez (standing) checks in with Operator Joe Hidalgo in the control room
Over in the control room, Operator Joe Hidalgo sits in front of a mimic panel, an aptly named electronic map that mimics all of the operations going on throughout McDonald Island. His job involves monitoring the entire facility and keeping a close eye out for any potential anomalies. Between the gas pressure regulation, the various chemicals used to treat the gas, the dehydration system that can get as hot as 1,500 degrees Fahrenheit, and all the other equipment in operation on a daily basis, careful monitoring and attention to detail is key for the plant’s overall safety, as well as the safety of the employees.
In fact, safety plays a huge role in the jobs that all the McDonald Island employees do. From the leak surveyors to the operators and technicians, every Local 1245 member at McDonald Island has to consider both their own safety, as well as the public’s safety, in the work that they do each day. For example, given that fact that natural gas is odorless, colorless and tasteless, the workers at McDonald Island are tasked with infusing the gas with Mercaptan, an additive that gives off the sulfuric odor that most people commonly recognize as “gas smell.” The addition of Mercaptan to the gas is critical for safety, ensuring that even the smallest of gas leaks can be detectable by scent alone.
Mercaptan is just one example of the countless safety-oriented processes that occur at McDonald Island every day. Natural gas may get a bad rap sometimes, but the truth is that gas power plays a key role in California’s transition to more renewable energy, and the Local 1245 members at McDonald Island pride themselves on the work they do to contribute to a safe and reliable pipeline.
–Rebecca Band, IBEW 1245 Communications Director
Photos by John Storey